TheGermanEngineer
BIOS-Overclocker(in)
Hallo,
ja da bin ich wieder. Derjenige, der sich seine Cases prinzipiell selbst baut. Ihr wisst nicht, wovon ich rede? Take a look here! Das Ganze geht nun in die zweite Runde. Das Case wird nicht für mich sein, bleibt aber im Familienkreis.
Beim Konzept wird es einige Änderungen geben. Finanziell besteht größerer Spielraum, daher kann durch den Einsatz von weiteren SFX-Komponenten und dem Verzicht auf eine HDD das Volumen deutlich reduziert werden. Ungefähr 12,5 L sind dabei angepeilt. Das vorherige Projekt hatte noch ein Volumen von etwas über 21 L.
Komponenten sind größtenteils noch nicht vorhanden, aber schon prinzipiell festgelegt:
CPU: AMD Ryzen 5 5600X
Mainboard: Gigabyte B550I Aorus Pro AX
DRAM: 2x16 GB Patriot Viper 4 Blackout DDR4-3600 18-22-22-42
Kühler: Noctua NH-L12S mit Noctua NF-A12x25
GPU:AMD Radeon RX 6800 16 GB AMD Radeon RX 6700XT 12 GB
PSU: Corsair SF600 Platinum
SSD: Samsung 970 Evo Plus 1 TB + Crucial MX500 500 GB
Inhaltsverzeichnis
1. Planung
Natürlich entsteht zunächst ein Plan in Fusion 360. Im Vergleich zum letzten Mal habe ich auch einiges dazugelernt und habe daher deutlich detailliertere Modelle angefertigt. Spezifikationen werde ich hier nicht noch einmal nennen, die findet ihr alle in Kapitel 2 des letzten Buildlogs. Ich habe darauf geachtet, dass ich mehr Features von Fusion 360 nutze, z.B. parametrisierte Modellierung und den Konstruktionsverlauf. Dadurch kann ich nachträglich Randparameter wie Länge, Breite, Höhe des Gehäuses sowie die Dicke des Materials anpassen, ohne wieder von vorn zu beginnen. Gerade die Länge ist abhängig von der GPU. Ursprünglich habe ich mit einer 3070 FE geplant. Da diese mit ihrer Speicherausstattung aber kaum sinnvoll erscheint, hat nun eine RX 6800 ihren Platz eingenommen. Kurze Versionen sind bisher nicht abzusehen, es ist ja teilweise schon schwierig noch Dual-Slot-Designs zu finden. Das Referenz-Design der RX 6800 scheint mir daher noch am sinnvollsten zu sein.
Das Gehäuse orientiert sich konzeptionell am NCase M1. Es wird also keine schräge Upside-Down-Spielerei wie beim letzten Mal. Das Netzteil befindet sich daher vorne im Gehäuse und wird per Riser-Kabel nach hinten mit Strom versorgt. Effektiv wird es so auf die angesprochenen 12,5 L kommen. Oben und unten wird ein Mesh zum Einsatz kommen, für die Seite habe ich an Akustikstoff aus dem HiFi-Bedarf gedacht. Durch das Airflow-Konzept benötigt das Case Frischluft von der Seite, da die Front geschlossen ist. Der Akustikstoff sollte einigermaßen blick- und staubdicht sein, aber dennoch genug Luft sowie etwaige Beleuchtung aus dem Inneren durchlassen. Ich denke, das könnte schon ganz gut aussehen.
Baulich möchte ich keine großen Experimente machen. Auf Gehrungen werde ich also wieder verzichten. Meinen bisheriger Prozess werde ich also beibehalten (Intel reference not intended).
Im Inneren wird jeder Kubikzentimeter so gut wie möglich ausgenutzt. Die GPU hat nach vorne noch etwas Platz, damit man sie einfacher ein- und ausbauen kann. Das ist bei mir leider wahnsinnig eng, was aber vor allem am dicken Dark Rock 3 liegen dürfte. Hier kommt mit dem Noctua NH-L12S der wahrscheinlich beste Top-Flow-Kühler zum Einsatz, der hier noch bequem Platz findet. Da noch genug Platz zur Seite vorhanden ist, soll vermutlich ein NF-A12x25 als Push agieren, beiliegend ist die schmalere 15mm-Variante. Ggf. kommen auch beide als Push/Pull-Konfiguration zum Einsatz, das werden dann die realen Temperaturen entscheiden. Ob der NF-A8 als Outtake dort bleiben wird ist ebenso offen. Auch hier möchte ich testen, ob er als Intake mehr Sinn ergibt oder lieber ganz weggelassen werden kann.
Abgesehen davon sind keine weiteren Lüfter geplant. Die GPU wird auch hier eigenständig für Intake verantwortlich sein, oben könnte man zur Not noch schmale 15mm-Lüfter verbauen. Der Netzteillüfter sollte aber auch für etwas Airflow sorgen.
Auf der Rückseite können bis zu zwei 2,5"-Laufwerke ihren Platz finden . Zunächst ist dort nur eine MX500 geplant, es ist also noch Platz für Upgrade. Die SSD-Bracket wird aus Aluminium bestehen. Unten ist eine Kabeldurchführung vorhanden. Oben ist ein Teil der PSU-Bracket zu sehen, die auch von der Rückseite verschraubt wird. Auch sie besteht aus Aluminium.
Und zu guter Letzt noch ein Renderbild von oben mit einigen entfernten Gehäuseteilen. So wird vielleicht etwas klarer, wie die Hardware im Inneren platziert ist. Besonders stolz bin ich hier auf den NH-L12S. Es hat mich einige Zeit gekostet, aber es dürfte mittlerweile zu meinen detailliertesten Komponenten gehören.
Weiter geht es dann mit dem Anfertigen erster Teile. Einige Dinge müssen noch besorgt werden, anderes ist schon hier. Es geht auf jeden Fall in Kürze weiter.
ja da bin ich wieder. Derjenige, der sich seine Cases prinzipiell selbst baut. Ihr wisst nicht, wovon ich rede? Take a look here! Das Ganze geht nun in die zweite Runde. Das Case wird nicht für mich sein, bleibt aber im Familienkreis.
Beim Konzept wird es einige Änderungen geben. Finanziell besteht größerer Spielraum, daher kann durch den Einsatz von weiteren SFX-Komponenten und dem Verzicht auf eine HDD das Volumen deutlich reduziert werden. Ungefähr 12,5 L sind dabei angepeilt. Das vorherige Projekt hatte noch ein Volumen von etwas über 21 L.
Komponenten sind größtenteils noch nicht vorhanden, aber schon prinzipiell festgelegt:
CPU: AMD Ryzen 5 5600X
Mainboard: Gigabyte B550I Aorus Pro AX
DRAM: 2x16 GB Patriot Viper 4 Blackout DDR4-3600 18-22-22-42
Kühler: Noctua NH-L12S mit Noctua NF-A12x25
GPU:
PSU: Corsair SF600 Platinum
SSD: Samsung 970 Evo Plus 1 TB + Crucial MX500 500 GB
Inhaltsverzeichnis
- Planung
- Einzelteile
- Zusammenbau Teil 1
- Zusammenbau Teil 2 und Verkabelung
- Eingeholt von der Realität
- Hardware zieht ein
- Glück muss man haben
1. Planung
Natürlich entsteht zunächst ein Plan in Fusion 360. Im Vergleich zum letzten Mal habe ich auch einiges dazugelernt und habe daher deutlich detailliertere Modelle angefertigt. Spezifikationen werde ich hier nicht noch einmal nennen, die findet ihr alle in Kapitel 2 des letzten Buildlogs. Ich habe darauf geachtet, dass ich mehr Features von Fusion 360 nutze, z.B. parametrisierte Modellierung und den Konstruktionsverlauf. Dadurch kann ich nachträglich Randparameter wie Länge, Breite, Höhe des Gehäuses sowie die Dicke des Materials anpassen, ohne wieder von vorn zu beginnen. Gerade die Länge ist abhängig von der GPU. Ursprünglich habe ich mit einer 3070 FE geplant. Da diese mit ihrer Speicherausstattung aber kaum sinnvoll erscheint, hat nun eine RX 6800 ihren Platz eingenommen. Kurze Versionen sind bisher nicht abzusehen, es ist ja teilweise schon schwierig noch Dual-Slot-Designs zu finden. Das Referenz-Design der RX 6800 scheint mir daher noch am sinnvollsten zu sein.
Das Gehäuse orientiert sich konzeptionell am NCase M1. Es wird also keine schräge Upside-Down-Spielerei wie beim letzten Mal. Das Netzteil befindet sich daher vorne im Gehäuse und wird per Riser-Kabel nach hinten mit Strom versorgt. Effektiv wird es so auf die angesprochenen 12,5 L kommen. Oben und unten wird ein Mesh zum Einsatz kommen, für die Seite habe ich an Akustikstoff aus dem HiFi-Bedarf gedacht. Durch das Airflow-Konzept benötigt das Case Frischluft von der Seite, da die Front geschlossen ist. Der Akustikstoff sollte einigermaßen blick- und staubdicht sein, aber dennoch genug Luft sowie etwaige Beleuchtung aus dem Inneren durchlassen. Ich denke, das könnte schon ganz gut aussehen.
Baulich möchte ich keine großen Experimente machen. Auf Gehrungen werde ich also wieder verzichten. Meinen bisheriger Prozess werde ich also beibehalten (Intel reference not intended).
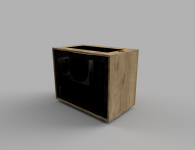
Im Inneren wird jeder Kubikzentimeter so gut wie möglich ausgenutzt. Die GPU hat nach vorne noch etwas Platz, damit man sie einfacher ein- und ausbauen kann. Das ist bei mir leider wahnsinnig eng, was aber vor allem am dicken Dark Rock 3 liegen dürfte. Hier kommt mit dem Noctua NH-L12S der wahrscheinlich beste Top-Flow-Kühler zum Einsatz, der hier noch bequem Platz findet. Da noch genug Platz zur Seite vorhanden ist, soll vermutlich ein NF-A12x25 als Push agieren, beiliegend ist die schmalere 15mm-Variante. Ggf. kommen auch beide als Push/Pull-Konfiguration zum Einsatz, das werden dann die realen Temperaturen entscheiden. Ob der NF-A8 als Outtake dort bleiben wird ist ebenso offen. Auch hier möchte ich testen, ob er als Intake mehr Sinn ergibt oder lieber ganz weggelassen werden kann.
Abgesehen davon sind keine weiteren Lüfter geplant. Die GPU wird auch hier eigenständig für Intake verantwortlich sein, oben könnte man zur Not noch schmale 15mm-Lüfter verbauen. Der Netzteillüfter sollte aber auch für etwas Airflow sorgen.
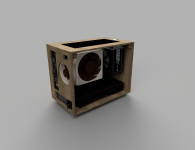
Auf der Rückseite können bis zu zwei 2,5"-Laufwerke ihren Platz finden . Zunächst ist dort nur eine MX500 geplant, es ist also noch Platz für Upgrade. Die SSD-Bracket wird aus Aluminium bestehen. Unten ist eine Kabeldurchführung vorhanden. Oben ist ein Teil der PSU-Bracket zu sehen, die auch von der Rückseite verschraubt wird. Auch sie besteht aus Aluminium.
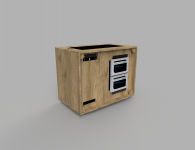
Und zu guter Letzt noch ein Renderbild von oben mit einigen entfernten Gehäuseteilen. So wird vielleicht etwas klarer, wie die Hardware im Inneren platziert ist. Besonders stolz bin ich hier auf den NH-L12S. Es hat mich einige Zeit gekostet, aber es dürfte mittlerweile zu meinen detailliertesten Komponenten gehören.
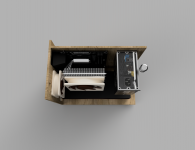
Weiter geht es dann mit dem Anfertigen erster Teile. Einige Dinge müssen noch besorgt werden, anderes ist schon hier. Es geht auf jeden Fall in Kürze weiter.
Zuletzt bearbeitet: